In the rapidly evolving landscape of industrial automation and motor-driven systems, the demand for reliable, precise, and durable testing equipment has never been higher. Companies across industries rely on cutting-edge technologies to ensure their motors and mechanical systems operate at peak performance. Among the most critical tools in this domain are hysteresis brakes, hysteresis dynamometers, hysteresis clutches, and integrated motor test systems. These devices form the backbone of modern quality assurance, enabling engineers to validate efficiency, durability, and compliance with stringent industry standards.
The Science Behind Hysteresis Technology
At the core of hysteresis-based devices lies a fascinating electromagnetic principle. Unlike traditional friction-based systems, hysteresis brakes and clutches utilize magnetic fields to generate torque through the hysteresis loss phenomenon in specially designed rotor materials. This contactless operation eliminates mechanical wear, ensuring consistent performance over extended periods. For instance, hysteresis dynamometers provide unparalleled accuracy in measuring torque and rotational speed without physical contact, making them ideal for testing high-speed motors in aerospace or electric vehicle applications.
Motor Dynamometers: The Heart of Performance Validation
Modern motor dynamometers have evolved into sophisticated systems capable of simulating real-world operating conditions. By pairing hysteresis brakes with advanced control software, these units can replicate dynamic loads ranging from sudden torque spikes in industrial machinery to gradual resistance changes in renewable energy systems. A key advantage lies in their bidirectional testing capability—whether evaluating regenerative braking in EVs or assessing motor-generator sets for wind turbines, these systems deliver data-rich insights into energy efficiency and thermal management.
Hysteresis Clutches: Precision in Motion Control
In applications requiring smooth torque transmission and precise slip control, hysteresis clutches outperform conventional mechanical counterparts. Their ability to maintain consistent torque regardless of rotational speed makes them invaluable in packaging machinery, textile manufacturing, and precision robotics. Recent advancements include integrated temperature compensation systems that maintain torque accuracy within 0.5% even during prolonged operation, addressing a critical need in semiconductor manufacturing equipment where micron-level precision is non-negotiable.
Integrated Motor Test Systems: Beyond Component Testing
Leading-edge motor test equipment now combines multiple technologies into unified platforms. A typical motor test system might incorporate:
- Hysteresis-based loading units for dynamic performance validation
- Multi-channel data acquisition systems sampling at 1MHz+ frequencies
- Environmental chambers for thermal stress testing (-40°C to +200°C)
- AI-powered analytics software for predictive maintenance modeling
These systems enable comprehensive evaluation of everything from miniature drone motors to multi-megawatt industrial drives. A notable case study involves an automotive supplier reducing prototype validation time by 68% through automated test sequences that simultaneously measure electrical, mechanical, and thermal parameters.
Industry-Specific Applications
The versatility of hysteresis-based testing solutions spans numerous sectors:
Electric Vehicle Development
Engineers leverage hysteresis dynamometers to simulate diverse driving conditions while measuring:
- Battery-to-wheel energy efficiency
- Regenerative braking performance
- Thermal runaway thresholds
- NVH (Noise, Vibration, Harshness) characteristics
Aerospace and Defense
Certification-grade test systems employ redundant hysteresis brakes to validate:
- Actuator response times under extreme G-forces
- Generator load rejection capabilities
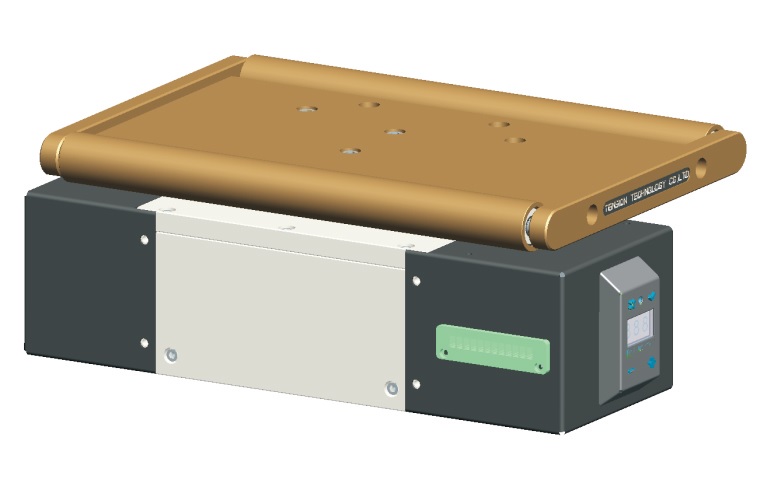
- Long-duration endurance testing for UAV propulsion systems
Industrial Automation
Motor test benches equipped with programmable hysteresis loads help optimize:
- Servo motor positioning accuracy
- Conveyor system energy consumption
- Robotic arm repeatability under variable payloads
Emerging Trends in Testing Technology
As industries push towards smarter manufacturing, several innovations are reshaping motor testing:
1. IoT-Enabled Predictive Maintenance
Wireless torque sensors integrated with hysteresis dynamometers now provide real-time cloud-based monitoring, enabling predictive maintenance algorithms to detect bearing wear or winding insulation degradation weeks before failure occurs.
2. High-Speed Testing for Micro-Motors
With the proliferation of miniaturized motors in medical devices and consumer electronics, test systems now achieve 500,000 RPM measurement capabilities while maintaining 0.01% torque resolution.
3. Energy Recovery Systems
Next-generation dynamometers incorporate regenerative power absorption, converting mechanical energy during braking phases into usable electricity—some facilities report 40% reductions in testing facility energy costs.
4. Digital Twin Integration
Advanced motor test platforms now synchronize with digital twin models, allowing virtual-physical hybrid testing. This approach enables engineers to validate control algorithms against simulated mechanical loads before physical prototypes exist.
Selecting the Right Testing Solution
When investing in motor test equipment, consider these critical factors:
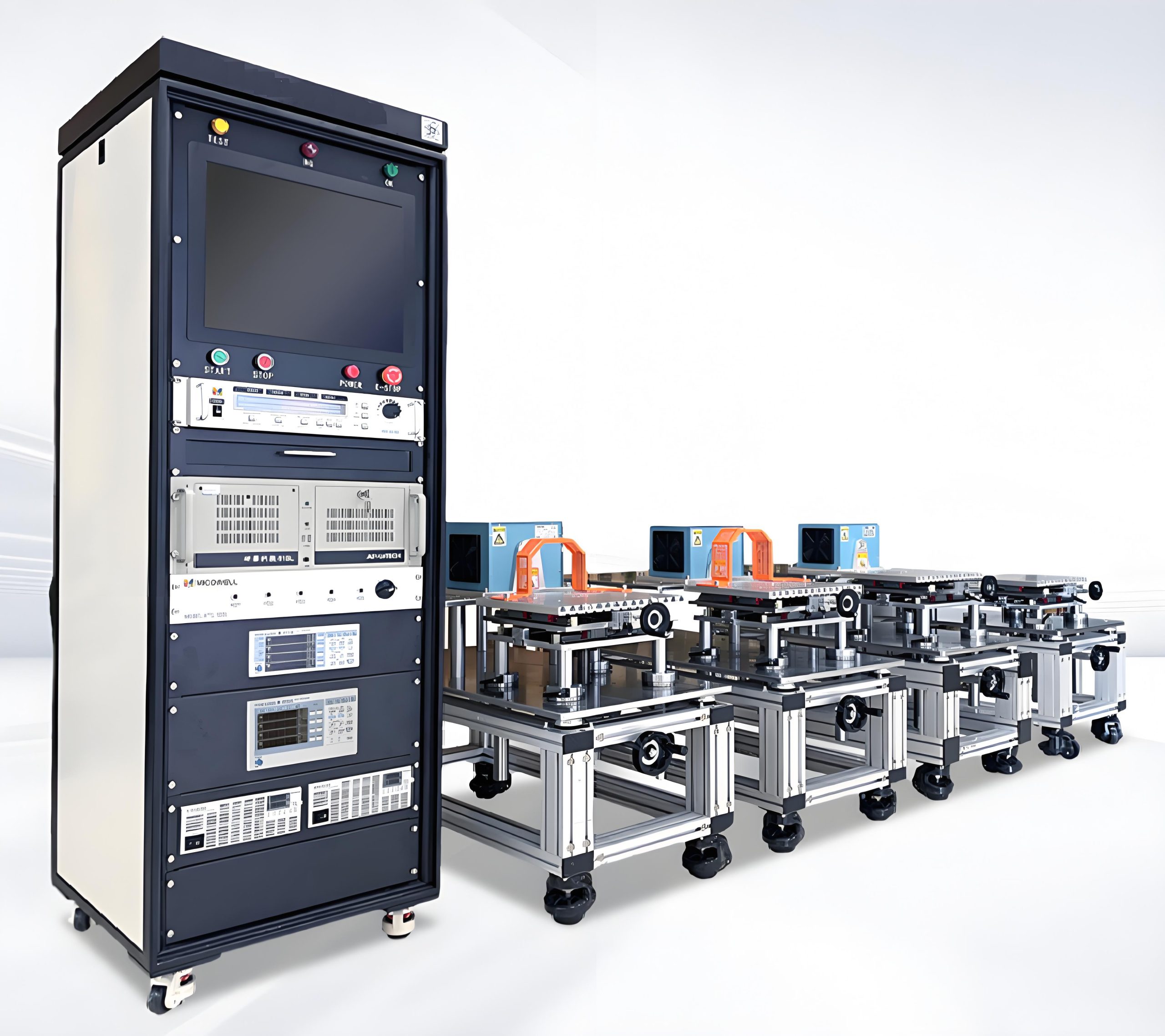
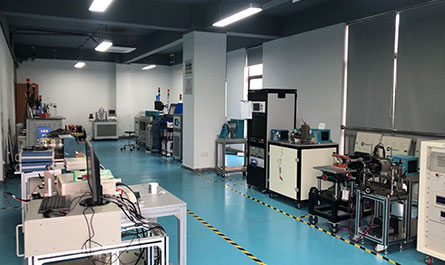
Torque Range and Accuracy
Ensure the system covers both startup torque (critical for HVAC compressors) and maximum operational torque with appropriate safety margins. Look for hysteresis brakes offering at least 0.1% full-scale accuracy.
Dynamic Response Characteristics
For testing servo motors or robotics, prioritize systems with torque response times under 5 milliseconds. Variable inertia simulation capabilities are essential for automotive transmission testing.
Software Ecosystem
Evaluate whether the control software supports:
- Custom test profile programming
- Real-time FFT analysis for vibration diagnostics
- Direct export to CAE tools like ANSYS or Simulink
Compliance Certifications
Industry-specific standards such as ISO 17025 for calibration or IEC 60034-30-2 for motor efficiency grading may dictate required accreditations for your test equipment.
Future-Proofing Considerations
Modular architectures allow gradual upgrades—opt for systems supporting:
- Additional sensor channels
- Higher voltage/current ratings
- Compatibility with emerging communication protocols like OPC UA
Conclusion
In an era where motor efficiency directly impacts operational costs and environmental compliance, investing in advanced hysteresis-based testing solutions is no longer optional—it’s a strategic imperative. From precision hysteresis clutches ensuring smooth production line operations to full-scale motor test systems validating next-generation EV powertrains, these technologies form the invisible backbone of quality assurance across industries.
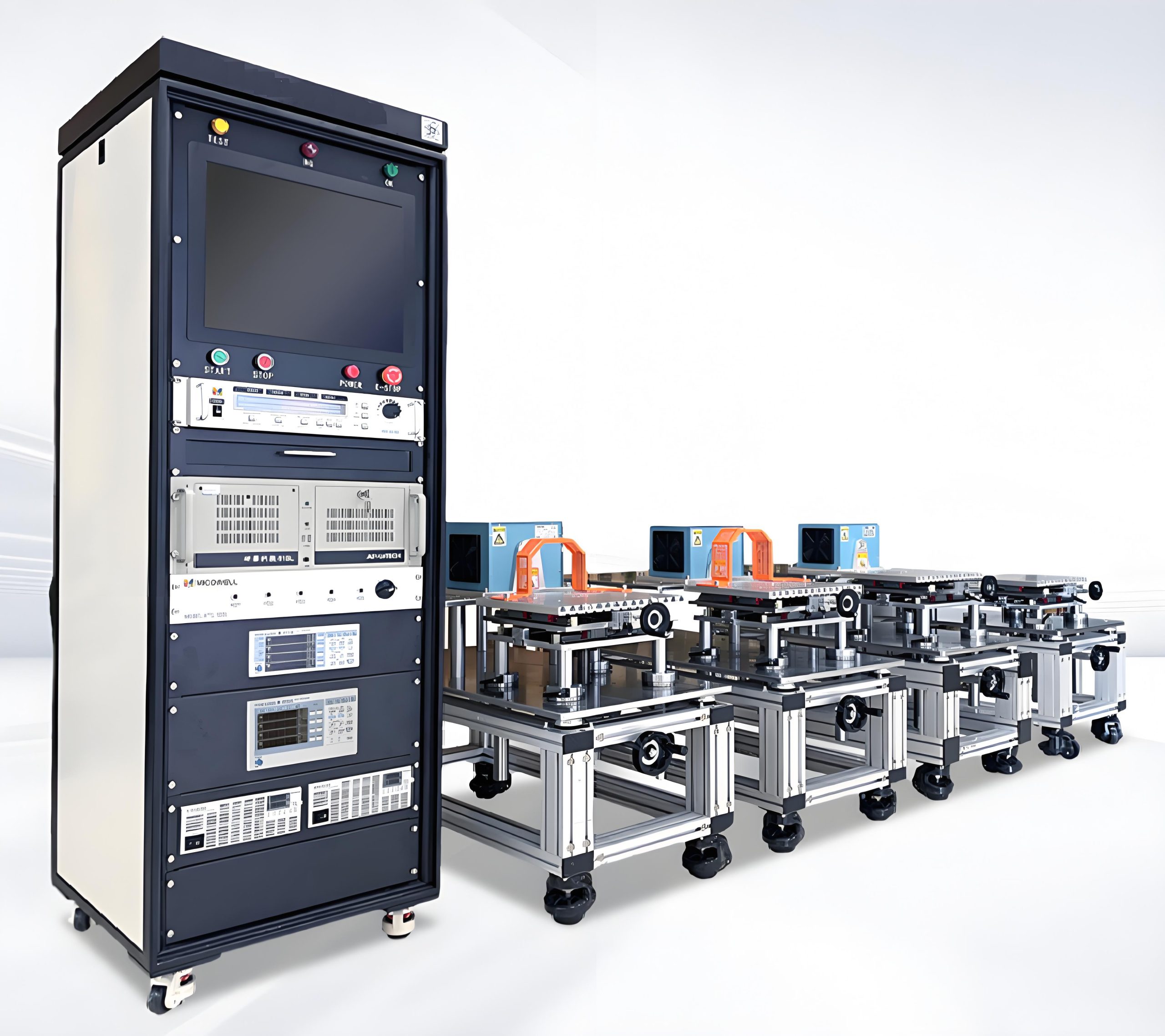
As you evaluate testing solutions, prioritize partners offering not just hardware, but complete ecosystems combining robust equipment with intelligent software and industry-specific expertise. No-load performance evaluation will not only catch defects but provide actionable insights to drive continuous improvement in motor design, manufacturing processes, and ultimately, end-product performance.
Whether you’re optimizing miniature motors for wearable devices or testing multi-megawatt generators for wind farms, remember: the precision of your measurements today determines the competitiveness of your products tomorrow. Embrace the power of hysteresis technology and advanced motor testing systems to stay ahead in the global engineering race.